Reload Annealer Auto Feeder Compete
• Reload Annealer
• 2 X Case Trays
RELOAD ANNEALER
Easy
Reload Annealer is extremely easy to setup in 3 simple steps and to operate using the Reloading Technology App.
Quick
Setting up the Reload Annealer and changing from one calibre to the next can be done in under one minute without sacrificing any valuable brass.
Consistent
The Induction coil height is automatically set to within 1mm and the annealing time to within 1 millisecond every time.
- Easy to assemble and setup.
- Easy to change from one case size to another.
- Can anneal cases from .22Hornet to 505 Gibbs.
- Quick, cases annealed in 2-3 seconds.
- Up to 800 cases annealed per hour.
- Fully automated case feeder, no other equipment required.
- Extremely Accurate – to within in 1mm and 1 millisecond.
- Setup using the Reloading Technology App on your phone.
- Annealing data for all known cases available on the App.
- Consistent results every time.
- Safe – no open flame, no need to handle hot cases.
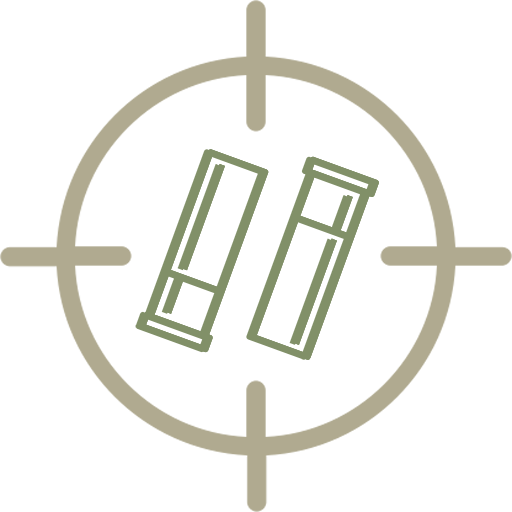
ANNEALER Assembly
Case feeder installation
Case feeder assembly
Installation of the App
Assembling the RELOAD ANNEALER case annealer is easy. The legs are installed under the body and the RELOAD CASE FEEDER is simply clipped and secured on to the top of the unit. Plug in the power cord (220v and 110v ready).
Select the case plate for your calibre and adjust the case length gage on the feeder.
Select the calibre from the App and the RELOAD ANNEALER automatically sets the coil to the correct height and accurately calculates and sets the annealing time.
Press “go” on the App and the RELOAD ANNEALER automatically starts to anneal the cases in the hopper.
When all the cases have all been annealed, the RELOAD ANNEALER will automatically turn off and notify you via the App that the annealing has been completed.
Our assembly videos include:
- ANNEALER Assembly
- Case feeder installation
- Case feeder assembly
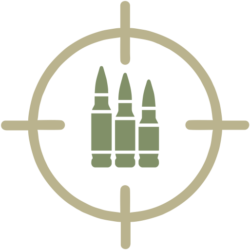
Induction annealing is the process of softening the necks of cases, through heating in an electrically contactless manner. This is achieved through placing the cases within a magnetic field, which induces eddy currents within the brass. Technically, the lower the resistivity of the brass, or the higher the intensity of the magnetic field, the greater are the eddy currents and, consequently, the greater the heating effect. There is no heating element as such; the only thing to get hot is the case. The magnetic field is focussed to maximise the eddy currents and heating in the location where it is specifically required, i.e. the neck and shoulder.
Reviews
There are no reviews yet.